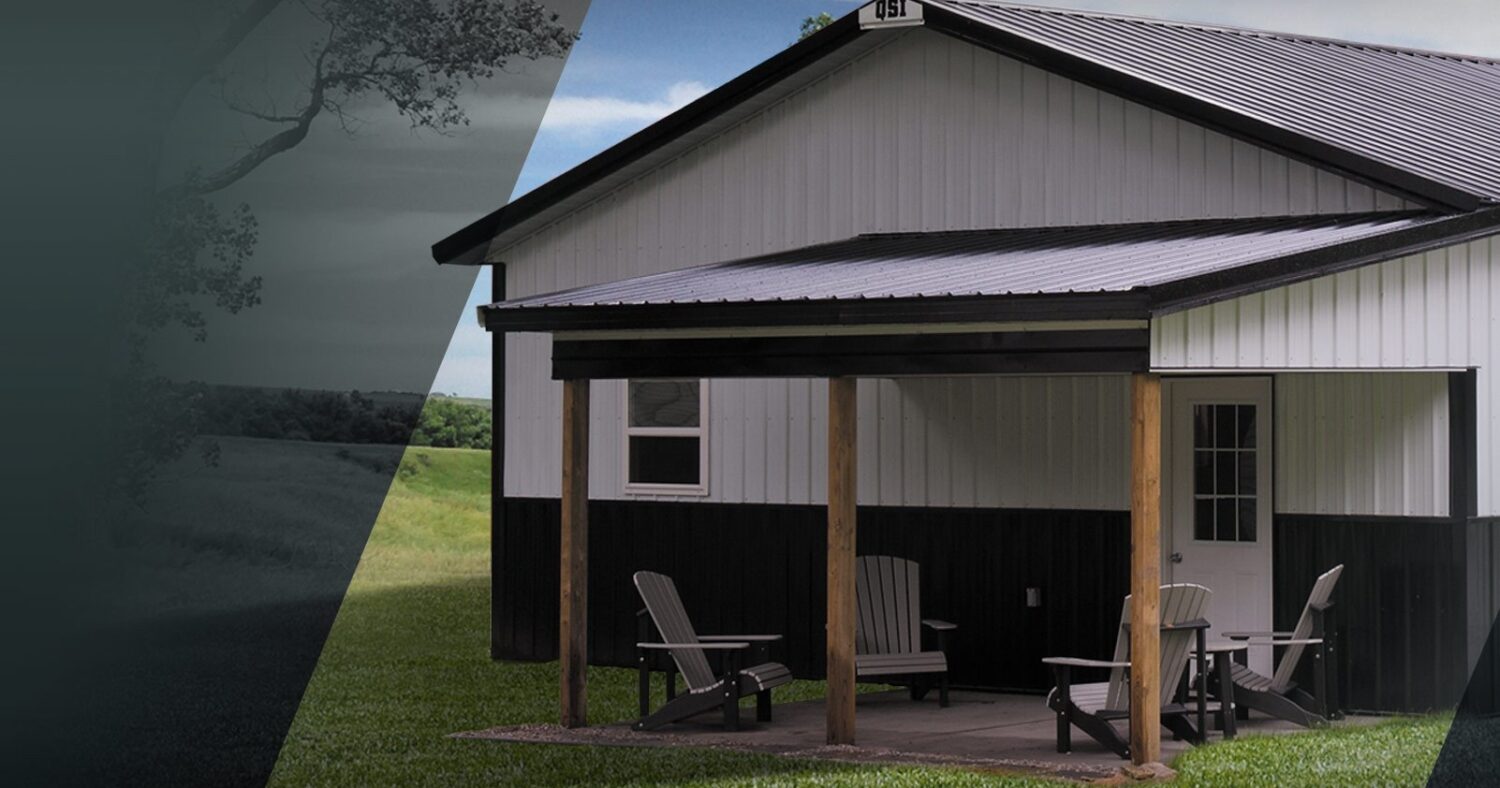
Condensation in Post-Frame Buildings: A Midwest Perspective
Condensation is a common yet often misunderstood challenge in post-frame buildings, particularly during the Midwest's notorious cold snaps. It’s important to recognize that condensation is not an insulation problem or a flaw in the building itself; it’s a moisture issue. Understanding what causes condensation, how it impacts your building, and how to prevent it can protect your investment and keep your space functional.
What Is Condensation?
Condensation occurs when warm, moist air interacts with a cold surface, cooling the air and causing moisture to condense into water droplets. This phenomenon happens because warmer air holds more moisture than cooler air. When the air temperature drops, its capacity to retain moisture decreases, leading to condensation. A familiar example is the water droplets that form on a glass of ice water on a humid summer day.
In post-frame buildings, condensation is most noticeable on inside surfaces like ceilings, windows, skylights, and roof hatches—areas where warm indoor air meets colder external temperatures.
Why Does Condensation Happen in Winter?
Condensation is more frequent in winter due to the stark temperature differences between the warm, moist interior of a building and the frigid exterior. Large temperature swings during Midwest winters exacerbate the problem, especially during sudden transitions from mild weather to freezing temperatures. These swings create ideal conditions for condensation as the rapid cooling causes moisture-laden air to deposit water onto cold surfaces.
Sources of Moisture
Moisture inside post-frame buildings often comes from various sources, including:
- Livestock and manure
- Non-vented heating systems (e.g., propane or kerosene heaters)
- Freshly poured concrete
- Concrete contains approximately 16% water and releases moisture as it cures, at a rate of 0.1 pounds per square foot per hour. This process can take up to a month.
- Thawing snow from vehicles
- Wet fill materials around the building site, which can take six months or more to dry.
Remember, these moisture sources are cumulative, meaning even small contributions can lead to significant humidity problems over time. For example, a combination of thawing snow from vehicles, moisture released from curing concrete, and unvented heating systems can create a highly humid environment, significantly increasing condensation risks.
Preventing Condensation in Your Post-Frame Building
- Limit Humidity Sources
- Dry equipment and vehicles before storing them.
- Squeegee out melted snow or ice from the floor.
- Address puddles near the building’s perimeter.
- Improve Ventilation
- Use ridge vents and vented eave soffits to facilitate airflow.
- Open windows and doors when possible to exchange moist air for drier outdoor air.
- Run a dehumidifier during the winter or damp weather.
- Insulate and Add Vapor Barriers
- Insulation reduces temperature differences and prevents cold surfaces from forming. However, even with proper insulation, condensation can still occur if moisture levels are too high. This isn’t an insulation issue but rather a moisture problem. High humidity in the building can overwhelm the insulation’s ability to mitigate condensation, underscoring the importance of controlling moisture sources and improving ventilation.
- Install vapor barriers on the interior side of insulation to stop moisture from escaping into wall cavities.
- Control Heating Systems
- Avoid unvented heaters, as they release water vapor. For example:
- Propane heaters generate approximately 1 gallon of water vapor for every cubic foot of propane burned.
- Kerosene heaters release about 1.1 gallons of moisture per gallon of kerosene burned.
- Natural gas combustion produces about 1.25 gallons of moisture per 100 cubic feet of gas burned.
- Opt for electric or properly vented heating systems to maintain dry air.
- Avoid unvented heaters, as they release water vapor. For example:
- Monitor Humidity and Dew Point
- Use a hygrometer to track humidity levels. Aim for below 60% relative humidity to prevent condensation.
- Keep the interior temperature above the dew point to avoid condensation on cold surfaces.
- Manage Ground and Roof Moisture
- Use drainage systems to direct water away from the foundation.
- Install gutters and downspouts for effective roof runoff management.
- Apply floor coatings to limit moisture vapor from concrete floors.
Spotting and Addressing Condensation
Condensation often appears as "spot condensation" in areas with the most temperature variation, such as window corners, skylights, and roof hatches. These areas are prone to temperature variation because they are typically less insulated and more exposed to external weather conditions, allowing them to cool more rapidly than surrounding surfaces. Circulating air with fans or ventilation systems can reduce these localized issues. Similar to using a car’s defrost setting, air circulation evens out temperatures, minimizing condensation risks.
Midwest Cold Snaps and Condensation Risks
Buildings in the Midwest, especially larger structures with more internal air volume, are particularly vulnerable to condensation due to large temperature fluctuations and extreme winter lows. During sudden cold snaps, warm, moist air rises and meets the colder ceiling, leading to condensation. These conditions are also common in early spring when ground temperatures remain cool but atmospheric humidity increases.
Humidity Levels to Avoid Excessive Condensation
The following chart provides recommended indoor humidity levels based on outside temperatures to reduce condensation risks:
Outside Temperature (°F) | Recommended Indoor Humidity |
---|---|
-20°F or below | 15-20% |
-20°F to 10°F | 20-25% |
-10°F to 0°F | 25-30% |
0°F to 10°F | 30-35% |
10°F to 20°F | 35-40% |
Final Thoughts: Protect Your Building from Condensation
Condensation doesn’t have to be an ongoing issue in your post-frame building. By managing moisture sources, improving ventilation, and maintaining appropriate indoor temperatures, you can minimize condensation risks even during the Midwest’s harsh winters. These steps not only protect your building but also ensure a comfortable, dry space for years to come.
We understand that condensation control is a critical concern for post-frame buildings, and we want to provide accurate, reliable information. To reinforce the details we've shared, we’re linking to a peer-reviewed article from the National Frame Builders Association magazine. This article, written by industry professionals, confirms the key factors that influence condensation and effective solutions for prevention.
We stand by our commitment to sharing well-supported information, and we encourage you to review the research for yourself.
https://associationdatabase.co...